Five aims of manufacturing enterprises, that we help to achieve
- Production planning
- Production control (dispatching)
- Warehouse inventory management with regard to production orders
- Performing all types of accounting: financial, tax and management
- Product distribution (with the help of BIT.SuperAgent system)
To achieve these aims, we implement such instruments as:
- Multilevel sliding planning (SOP-MPS-RCCP-MRP-CRP-APSMES);
- Balancing capacities and resource needs;
- Calendar planning of production and procurements;
- Inventory management in manufacturing;
- Operative management of implementation of plans in manufacturing;
- Unified integrated system of manufacturing, material and labor accounting.
Among the key results, that our clients get, there are:
- Increase in production while using the same capacities;
- Reduction of production cycle;
- Achieving the set level of assets removed from circulation;
- Completion of production orders in time;
- Increased profitability of production.
Management of Production Processes with QlikView Business Analytics System
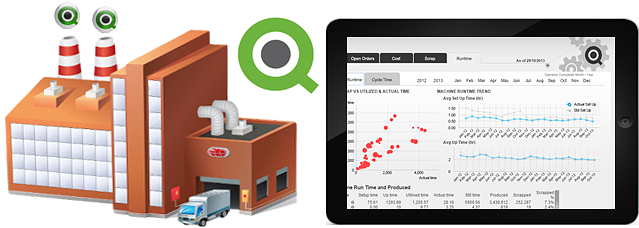
With the help of QlikView analytical system, the leading manufacturers of industrial products are able to achieve the following aims:
- to increase corporate management of risks, security and norm control;
- to form analytics and reports with the possibility to use the most complicated filters and groupings;
- to tie prices to the most important cost indicators, while preserving the profits;
- to see the structured, hierarchical description of nomenclature;
- to calculate the prime cost of production, the average daily stock balance and turnover;
- to get relevant information from the devices and react to changes promptly;
- to manage warehouse supply etc.
How to increase production using the same capacities and increase the enterprise’s profitability?
Automation of manufacturing enterprises has a number of distinctive features due to the industry specifics. The accurate planning of technological process and production capacity load are of great importance in manufacturing, especially in complex, multiconversion, assembling, per-order enterprises.
Of no less importance are the tasks of managing the product composition (constructive, technological, manufacturing) and also supplies, repairs, pricing.
It is necessary to control manufacturing at every stage of completion of production orders. Accounting processes also require close attention: it is necessary to keep accounts of raw material consumption, production in progress, production flaws, own and customer’s materials and stock, semi-finished products, finished products etc.
All these tasks are hard to fulfill, is there is no efficient data exchange between the departments or you have to process large amounts of information manually. You have to pay a high price for any error : even a inconspicuous mistake, for example, in calculating prime cost, may lead to great losses.
A modern IT-system will allow to exercise comprehensive control over manufacturing processes from taking materials into production till the finished product is released. At the same time:
- There will arise an opportunity to efficiently monitor the fulfillment of the production program - from the enlarged or shift production plans to the plans of completion of a separate order.
- You will be able to unify all the amount of normative reference information.
- The quality of planning and accounting of the finished product output will increase.
- The production order processing will become more efficient.
- There will be ensured the failure-proof provision of production facilities with materials and components.
- The accounting of raw materials and production in progress will become transparent.
- The plan and fact prime cost calculations will become more accurate, and you will be able to locate resources to reduce expenses and optimize expenditures.
- Production orders will be fulfilled in time.
- The exploitation of financial and material resources will be more rational and effective.
To achieve such results, it is necessary to fulfill the following 4 conditions
- An IT-system must comply with the specifics of the industry and be adjusted to the specifics of business-processes existing at your enterprise.
- An automation system must unite the operations of all the departments an subdivisions, ensuring transparency and efficient data exchange between all the participants of the process.
- Putting the solution into operation must be completed as soon and pain-free as possible.
- To avoid disappointments and financial losses, the automation should be performed by high-class specialists – your own (of they have enough expertise and experience) or third-party.
Choosing a partner for the realization of the project – measure thrice and cut once
- Our specialists are a strong project team with many years of experience in automation of manufacturing enterprises, each client with its own specifics and with production processes of any level of complexity.
- We automate enterprises of all the business spheres related to manufacturing: machinery production, metallurgy, construction supplies production, fuel and energy complex, food, agricultural, chemical, pharmaceutical industries etc.
- First BIT is a Center of Competence of 1C in manufacturing, and also a 1C’s partner in corporate projects.
- The responsibility for the project quality in our company lies on the universal Project Management Center, which collects and disseminates the best practices of business operation and automation.
- We implement complex manufacturing automation projects, which include all the specter of services – from the pre-project survey, modeling and reengineering of business-processes to setting up the system according to the specifics of your business.
- We will not leave you alone with the new system. We will provide maintenance of the newly created system , taking charge of supporting, updating it and ensuring its failure-proof operation. We will provide training and consultations for users and will help them with their further work with the programs.
- The development center of our company has released dozens of its own specialized software solutions, that are successfully used by thousands of manufacturing enterprises of Russia and the CIS countries.