Warehouse automation with RFID-technology
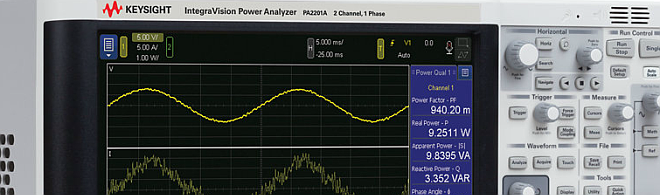
The Background
At the moment Keysight Technologies decided to collaborate with First BIT's International Department, it faced the task of increasing inventories management effectiveness.
Besides, the enterprise needed to organize constant operational control over inventories relocations in the warehouse and also reduce time and personnel expenses for collecting orders, inventarisation and examinations and also eliminate errors related to human factor.
The Project’s Technological Basis
The specialists of First Bit's International Department suggested using progressive RFID-technologies, allowing automation of quantity inventories accounting in Keysight Technologies’ warehouse without an operator, at the same time minimizing errors, caused by the “human element”.
For the accounting system the specialists of First BIT's International Department proprosed using “1C:Trade Management 8” software (version 11.1), and for the troubleproof functioning of RFID-equipment with accounting programm there was chosen “Cleverence: RFID for 1C: Enterprise” driver.
Combined use of these technological products of the leading providers in accounting sphere makes it possible to build an integrated system for accounting and control over inventories, that significantly increases the effectiveness of the warehouse functioning as a whole.
The Project’s Realization
Within the limits of the project for automation of inventories acounting in the warehouse of Keysight Technologies company in Russia, the specialists of First BIT's International Department have singled out and successfully completed the following 8 tasks:
1. Accounting of inventories supply to the company’s warehouse
- Revision of “Supply of goods and services” document with adding “Serial number” requisite.
- Adding “Barcode” column with automatic filling.
- Adding “Party number” column.
- Developing RFID-labels marking and programming with the possibility of bar-code printed on them.
2. Control over inventories discharge from the wareouse
- Formation of “Discharge Journal” document, fixing read-off RFID-code and the time of discharge.
- Adding “Responsible” for reading ACS card.
3. User identification for working with the inventories using ACS cards
- Connection nd settup of Proximity-reader with the use of ACS cards of the enterprise.
- Revision of “Individuals” directory for working with ACS cards.
4. Fixation of inventories delivery via the responsible person
- Formation of the “Relocation” document, containing the information about where the inventories are relocaed (to the warehouse, another legal entity etc.) with indication of the employee in charge of the inventories.
- Formation of the “Custody” document.
- Formation of different reports (on relocation etc.).
5. Fixation of inventories delivery without the responsible person
- Formation of the “payment voucher” document, fixing the information as from the ACS cards and without them.
- Development of automatic creation of payment voucher on the basis of the delivery for custody with triggering of RFID-system.
- Setup of automatic check of inventories available in the company’s warehouse.
6. Fixation of inventories supply to the warehouse
- Development of automatic check of inventories lacking in the warehouse with the triggering of RFID-gates.
- Setup of automatic formation of “Payment Voucher” document for goods.
7. Fixation of inventories for discharge either in the warehouse or with the responsible person
- Setting of inventories discharge, payment vouchers in document journal.
- Setting payment vouchers with the absent requisite “Employee”.
8. Asssembling and setting up of all the RFID-equipment, including:
- antennas for RFID-equpment with the right-handed and left-handed circle polarization,
- RFID-printers,
- RFID-labels,
- barcode scanners etc.
The Results
This Project was completed in 3 months.
The consultants of First BIT's International Department have achieved all the aims set at the outset of the project:
- thanks to the RFID-technology imeplementation the labor-expenditures for accounting in Keysight Technologies warehouse were reduced;
- time spent on controlling the warehouse operations was significantly reduced;
- there was an increase in the speed and accuracy of collecting orders;
- time spent on warehouse maintenance was greatly decreased, which had positive impact on the other business-processes of the company;
- the procees of inventarization and check-ups in the warehose was optimized and now hapens with greater speed;
- there have been developed and implemented automation procedures for different warehouse operations;
- there have been set up processes in the areas of more accurate and operative control over inventories movement and location in the warehouse.